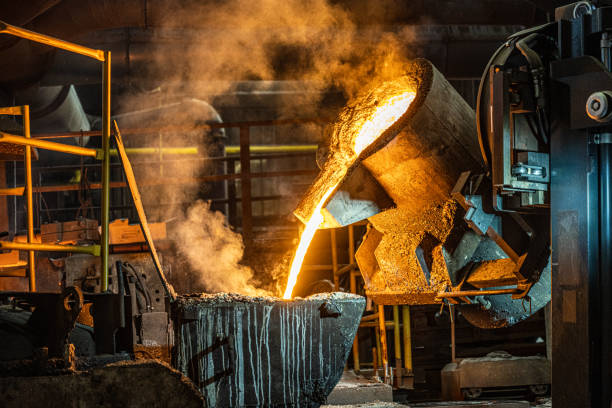
Introduction
The foundry industry is a crucial sector in manufacturing, where metal casting processes are employed to produce a wide range of components used in industries such as automotive, aerospace, construction, and machinery. Alloys play a significant role in foundries as they offer enhanced mechanical properties, corrosion resistance, and suitability for specific applications. This document explores different types of alloys used in foundry processes, their compositions, properties, and applications.
What Are Alloys?
An alloy is a mixture of two or more elements, where at least one is a metal. Alloys are developed to improve properties such as strength, hardness, ductility, and resistance to wear and corrosion compared to pure metals. In foundries, alloys are carefully selected based on the desired characteristics of the final product.
Types of Alloys Used in Foundry
1. Ferrous Alloys
Ferrous alloys contain iron as the primary element and are widely used in casting due to their excellent mechanical properties and cost-effectiveness. Common ferrous alloys include:
a) Cast Iron Alloys
Cast iron is a group of iron-carbon alloys with a carbon content greater than 2%. It is known for its excellent castability, wear resistance, and machinability. Types of cast iron alloys include:
Gray Cast Iron: Contains graphite flakes, which provide excellent damping properties and machinability. Used in engine blocks, pipes, and machine tool structures.
Ductile (Nodular) Iron: Contains spheroidal graphite, improving toughness and impact resistance. Used in automotive and heavy machinery components.
White Cast Iron: Contains cementite instead of graphite, making it hard and wear-resistant. Used in wear plates and grinding mills.
Malleable Cast Iron: A heat-treated form of white cast iron with improved ductility. Used in pipe fittings and railroad parts.
b) Steel Alloys
Steel alloys are iron-carbon alloys with controlled amounts of other elements to enhance properties.
Types include:
Carbon Steel: Contains varying carbon content to modify hardness and strength. Used in structural and industrial applications.
Stainless Steel: Contains chromium (at least 10.5%) for corrosion resistance. Used in food processing, medical devices, and marine applications.
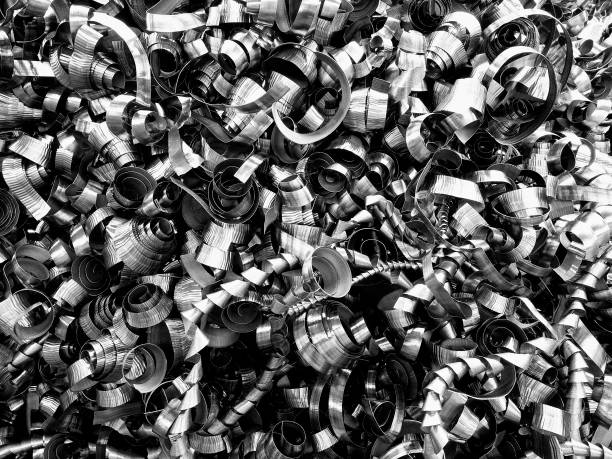
Tool Steel: Contains tungsten, molybdenum, and vanadium for high hardness and wear resistance. Used in cutting and forming tools.
High-Strength Low-Alloy (HSLA) Steel: Contains small amounts of alloying elements to improve strength without significant weight increase. Used in automotive frames and construction.
2. Non-Ferrous Alloys
Non-ferrous alloys do not contain significant amounts of iron, making them resistant to rust and corrosion. Common non-ferrous alloys include:
a) Aluminum Alloys
Aluminum alloys are lightweight, corrosion-resistant, and have excellent thermal and electrical conductivity. They are categorized into:
Cast Aluminum Alloys: Include silicon, copper, and magnesium to enhance strength and wear resistance. Used in automotive engine blocks and aerospace components.
Wrought Aluminum Alloys: Have high strength and formability, used in structural applications and packaging.
b) Copper-Based Alloys
Copper-based alloys are known for their high conductivity, corrosion resistance, and antimicrobial properties. Common types include:
Bronze (Copper-Tin Alloy): Used in bearings, marine components, and sculptures.
Brass (Copper-Zinc Alloy): Used in plumbing fixtures, musical instruments, and decorative items.
Beryllium Copper: Has high strength and conductivity, used in electrical contacts and aerospace applications.
c) Nickel Alloys
Nickel-based alloys offer excellent heat resistance, corrosion resistance, and strength at high temperatures. Examples include:
Inconel: Used in jet engines and power plants.
Monel: Resistant to seawater corrosion, used in marine engineering.
Hastelloy: Used in chemical processing industries.
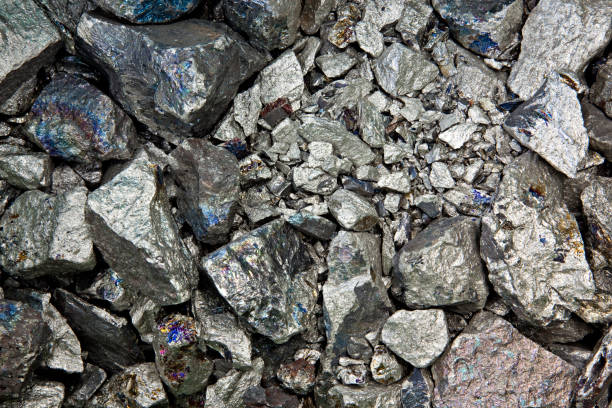
d) Titanium Alloys
Titanium alloys are strong, lightweight, and corrosion-resistant, making them suitable for aerospace, medical implants, and high-performance automotive parts.
e) Zinc and Magnesium Alloys
Zinc Alloys: Used in die casting for automotive and electronic components.
Magnesium Alloys: Extremely lightweight, used in aerospace and sporting goods.
Alloy Selection Criteria in Foundry
The choice of alloy in foundry applications depends on several factors:
Mechanical Properties: Strength, hardness, ductility, and toughness.
Corrosion Resistance: Suitability for harsh environments.
Wear Resistance: Ability to withstand friction and abrasion.
Machinability: Ease of cutting, shaping, and finishing.
Cost and Availability: Economic considerations in manufacturing.
Heat Resistance: Performance under high temperatures.
Foundry Casting Processes for Alloys
Different casting methods are used to produce alloy components:
Sand Casting: Used for ferrous and non-ferrous alloys, providing flexibility in size and shape.
Investment Casting: Produces high-precision parts, often used for aerospace and medical components.
Die Casting: Suitable for non-ferrous alloys like aluminum, zinc, and magnesium, producing high-volume, complex shapes.
Centrifugal Casting: Used for cylindrical components, common in pipe manufacturing.
Continuous Casting: Used for steel and non-ferrous metals, producing uniform material properties.
Applications of Foundry Alloys
Foundry alloys are used in various industries, including:
Automotive: Engine blocks, brake components, transmission parts.
Aerospace: Jet engine parts, structural components.
1. Ferrous Alloys
Ferrous alloys contain iron as the primary element and are widely used in casting due to their excellent mechanical properties and cost-effectiveness. Common ferrous alloys include:
a) Cast Iron Alloys
Cast iron is a group of iron-carbon alloys with a carbon content greater than 2%. It is known for its excellent castability, wear resistance, and machinability. Types of cast iron alloys include:
Gray Cast Iron: Contains graphite flakes, which provide excellent damping properties and machinability. Used in engine blocks, pipes, and machine tool structures.
Ductile (Nodular) Iron: Contains spheroidal graphite, improving toughness and impact resistance. Used in automotive and heavy machinery components.
White Cast Iron: Contains cementite instead of graphite, making it hard and wear-resistant. Used in wear plates and grinding mills.
Malleable Cast Iron: A heat-treated form of white cast iron with improved ductility. Used in pipe fittings and railroad parts.

b) Steel Alloys
Steel alloys are iron-carbon alloys with controlled amounts of other elements to enhance properties.
Types include:
Carbon Steel: Contains varying carbon content to modify hardness and strength. Used in structural and industrial applications.
Stainless Steel: Contains chromium (at least 10.5%) for corrosion resistance. Used in food processing, medical devices, and marine applications.
Tool Steel: Contains tungsten, molybdenum, and vanadium for high hardness and wear resistance. Used in cutting and forming tools.
High-Strength Low-Alloy Steel: Contains small amounts of alloying elements to improve strength without significant weight increase. Used in automotive frames and construction.
2. Non-Ferrous Alloys
Non-ferrous alloys do not contain significant amounts of iron, making them resistant to rust and corrosion. Common non-ferrous alloys include:
a) Aluminum Alloys
Aluminum alloys are lightweight, corrosion-resistant, and have excellent thermal and electrical conductivity. They are categorized into:
Cast Aluminum Alloys: Include silicon, copper, and magnesium to enhance strength and wear resistance. Used in automotive engine blocks and aerospace components.
Wrought Aluminum Alloys: Have high strength and formability, used in structural applications and packaging.
b) Copper-Based Alloys
Copper-based alloys are known for their high conductivity, corrosion resistance, and antimicrobial properties. Common types include:
Bronze (Copper-Tin Alloy): Used in bearings, marine components, and sculptures.
Brass (Copper-Zinc Alloy): Used in plumbing fixtures, musical instruments, and decorative items.
Beryllium Copper: Has high strength and conductivity, used in electrical contacts and aerospace applications.
c) Nickel Alloys
Nickel-based alloys offer excellent heat resistance, corrosion resistance, and strength at high temperatures. Examples include:
Inconel: Used in jet engines and power plants.
Monel: Resistant to seawater corrosion, used in marine engineering.
Hastelloy: Used in chemical processing industries.
d) Titanium Alloys
Titanium alloys are strong, lightweight, and corrosion-resistant, making them suitable for aerospace, medical implants, and high-performance automotive parts.
e) Zinc and Magnesium Alloys
Zinc Alloys: Used in die casting for automotive and electronic components.
Magnesium Alloys: Extremely lightweight, used in aerospace and sporting goods.
Alloy Selection Criteria in Foundry
The choice of alloy in foundry applications depends on several factors:
Mechanical Properties: Strength, hardness, ductility, and toughness.
Corrosion Resistance: Suitability for harsh environments.
Wear Resistance: Ability to withstand friction and abrasion.
Machinability: Ease of cutting, shaping, and finishing.
Cost and Availability: Economic considerations in manufacturing.
Heat Resistance: Performance under high temperatures.
Foundry Casting Processes for Alloys
Different casting methods are used to produce alloy components:
Sand Casting: Used for ferrous and non-ferrous alloys, providing flexibility in size and shape.
Investment Casting: Produces high-precision parts, often used for aerospace and medical components.
Die Casting: Suitable for non-ferrous alloys like aluminum, zinc, and magnesium, producing high-volume, complex shapes.
Centrifugal Casting: Used for cylindrical components, common in pipe manufacturing.
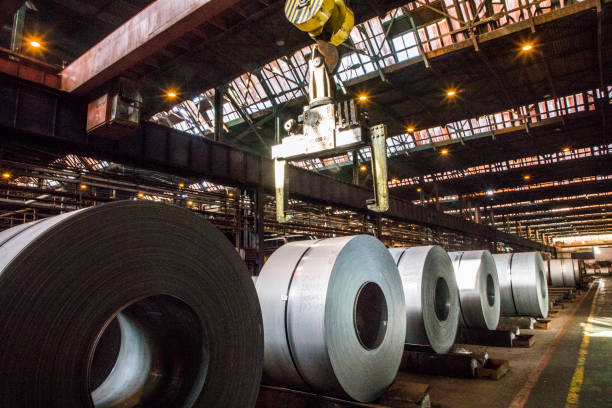
Continuous Casting: Used for steel and non-ferrous metals, producing uniform material properties.
Applications of Foundry Alloys
Foundry alloys are used in various industries, including:
Automotive: Engine blocks, brake components, transmission parts.
Aerospace: Jet engine parts, structural components.
Construction: Bridges, pipelines, structural beams.
Machinery: Gears, pumps, turbines.
Medical: Surgical instruments, implants.
Electronics: Electrical connectors, heat sinks. Bridges, pipelines, structural beams.
Machinery: Gears, pumps, turbines.
Medical: Surgical instruments, implants.
Electronics: Electrical connectors, heat sinks.